
Lindemann Silikon GmbH & Co.KG
Extrusion of silicone products
The Specialist in silicone
CALL NOWSilicone co-extrusion is a process that combines the versatile material silicone with the advanced technique of co-extrusion. But what does that mean exactly? Simply put, extrusion is the process of pushing a material through a shaped opening or die to form it. Co-extrusion, on the other hand, involves combining multiple materials into a single product. When these two methods are combined, they result in the production of unique and complex silicone products through the process of silicone co-extrusion. Let’s dive deeper into the world of silicone co-extrusion and explore what we can offer you.
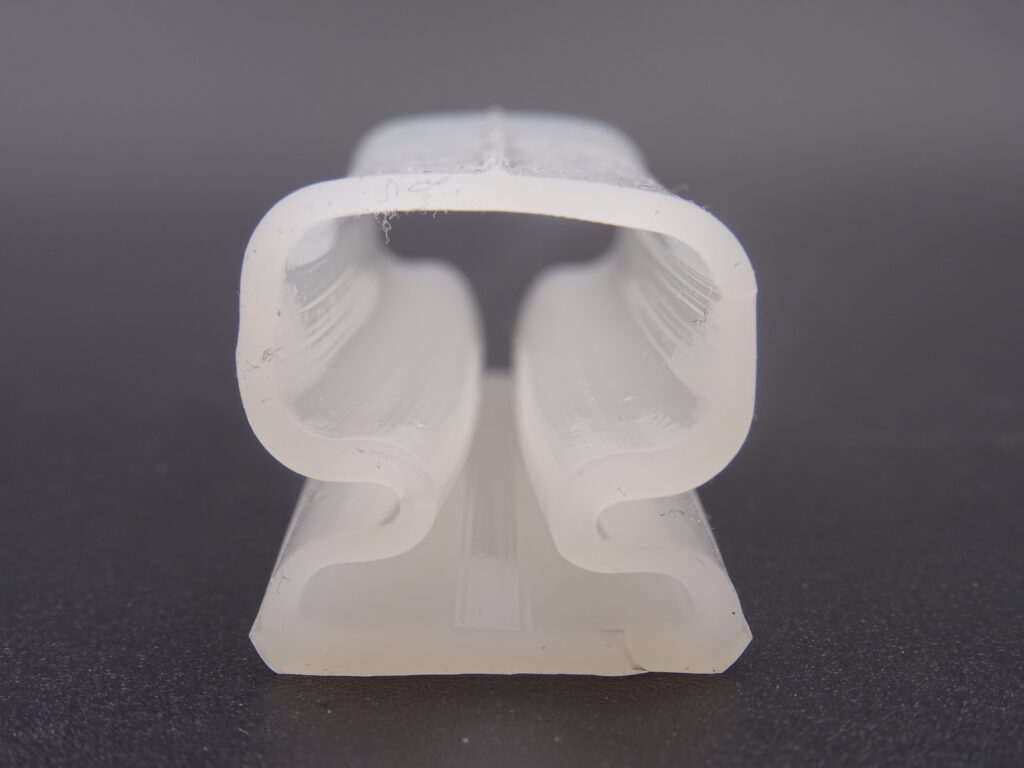
Understanding the Basics of Extrusion
Extrusion is a crucial manufacturing process in which silicone is pushed through a specially designed die or mold. This process shapes the silicone into various forms, such as tubes or profiles. The specific shape of the final product depends on the design of the die, highlighting the inherent adaptability and versatility of the extrusion process. Extrusion allows manufacturers to efficiently produce a wide range of uniform, high-quality silicone products.
What is Co-extrusion?
Co-extrusion is an advanced technique based on the process of extrusion. This method involves extruding two or more different materials through a single die to create a multi-layered product. Co-extrusion takes advantage of the unique properties of each type of silicone, producing a final product that combines the benefits of each material. Instead of forming just one type of silicone, co-extrusion merges various types into one. As a result, the final product exhibits a combination of advantageous properties, enhancing its functionality and usability. Essentially, co-extrusion not only maximizes the potential of silicone products but also elevates the possibilities of mechanical engineering to new heights.
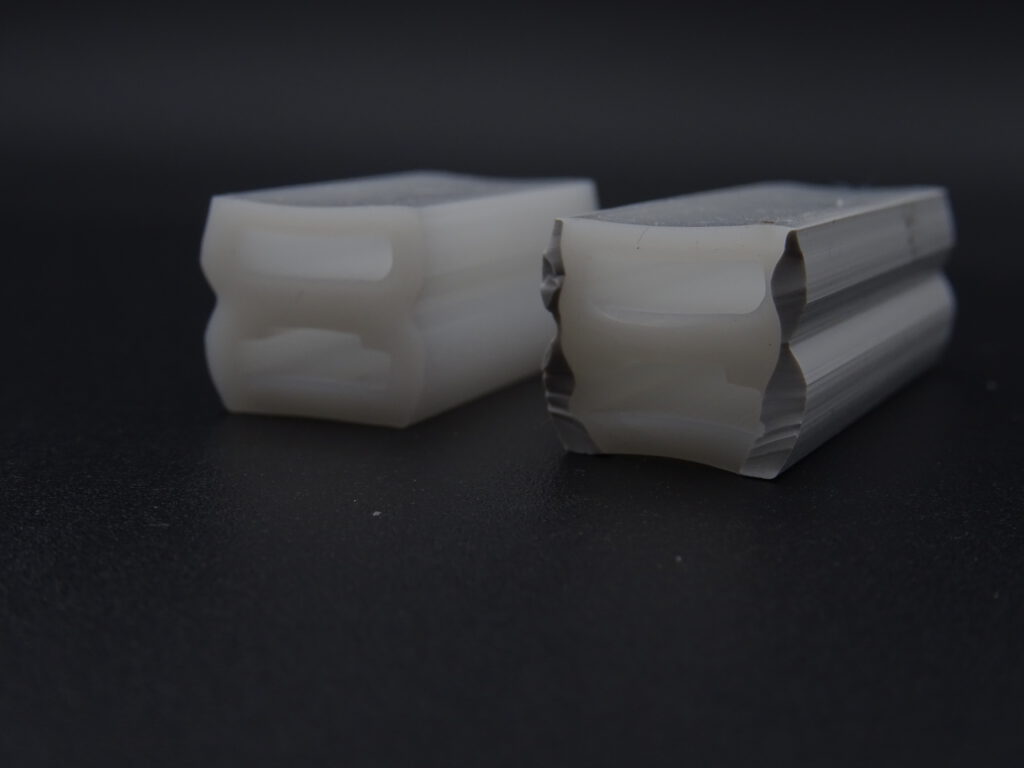
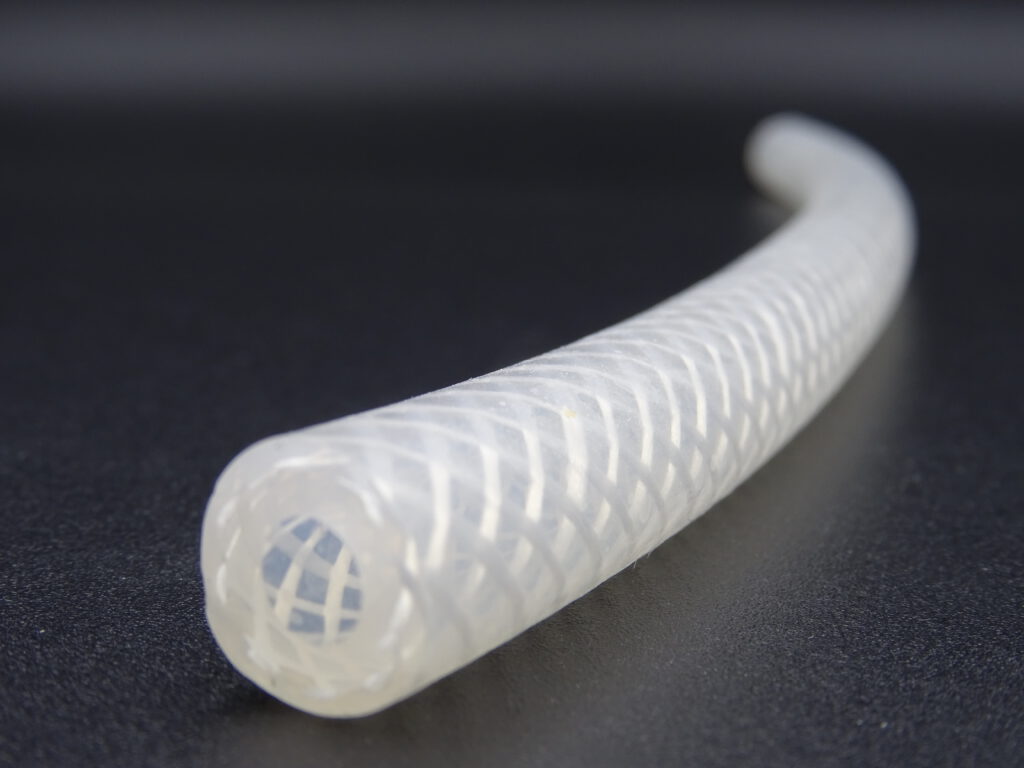
How Co-extrusion Works
Different types of silicone are loaded into separate hoppers to initiate the co-extrusion process. These materials are then subjected to a precisely controlled heating process and extruded under controlled pressure through a single die. This precise process enables the homogeneous bonding of various silicone types, resulting in a multi-layered end product. The material composition can be customized to harness the desired properties of each type of silicone. Through co-extrusion, products are created that combine advantageous features such as increased strength, improved durability, or resistance to specific environmental influences.
Silicone Products Manufactured Through Co-extrusion
The versatility of the co-extrusion process opens up a wealth of possibilities for producing high-performance silicone products. It paves the way for the development of a wide range of components used in various industries.
For example, the automotive industry relies on co-extruded silicone parts such as seals and profiles to enhance functionality and durability.
In the field of medical technology, co-extrusion has played a critical role. It is essential in manufacturing key devices such as catheters, which require the fusion of different types of silicone for optimal performance and patient safety.
Industrial applications also benefit significantly from co-extrusion. Examples include silicone hoses, profiles, and reinforced fabric hoses.läuche.
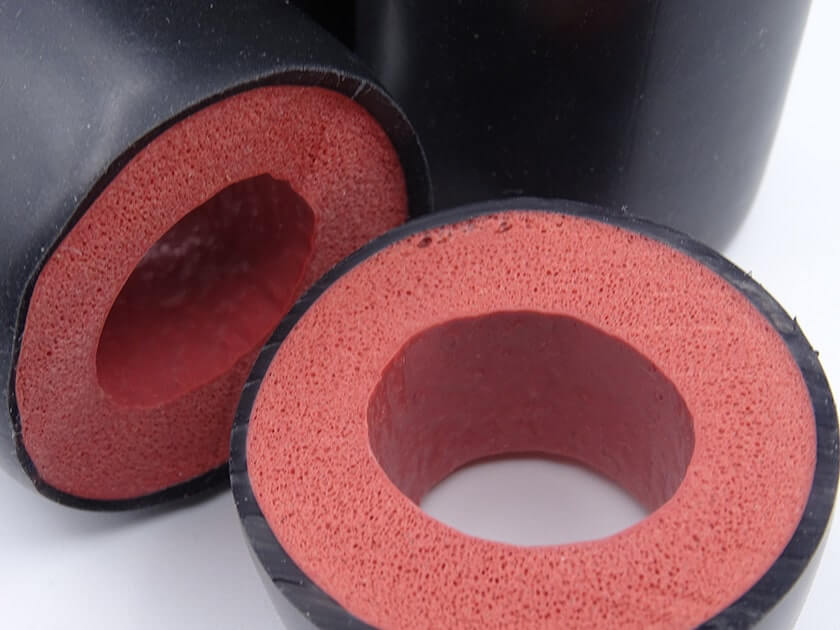
For your specific requirements in silicone co-extrusion, our experienced team is ready to assist you. We take pride in offering tailored solutions that balance efficiency, quality, and performance. Our commitment spans the entire process, from the earliest design stages to the final production phases. Contact us today to explore the many ways our top-notch co-extrusion capabilities can enhance your project.
Leave us a message, and we will get back to you!
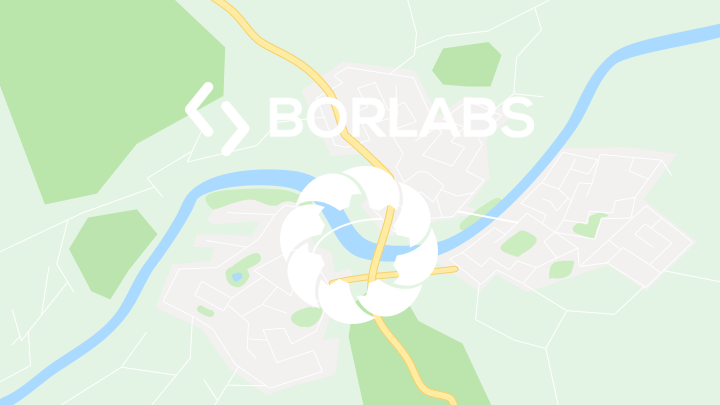
Mit dem Laden der Karte akzeptieren Sie die Datenschutzerklärung von Google.
Mehr erfahren